I’m sure many of you have noticed movies that replicate the patterns, plots, themes, and scenarios of the blockbuster shows. Today’s predictable formulae might involve guns, car chases, government conspiracies, and of course the 2 minutes of sexual this-or-that, never mind the plot. Another subtle pattern you’ve likely noticed is the role of the supporting hero; you know, the one who comes up with that tantalizing bit of information that seems to break the logjam of suspense. A long running favorite for this role is the computer geek/hacker who seems to easily penetrate any system and after a furious 100-words-per-minute staccato keyboard performance, the antagonists are as good as wet toast. Another emergent supporting-hero-favorite is the forensics expert. Of course, if the role is that of a computer forensics expert, the actor/actress will likely be up for an Academy Award. So, how about forensics for ESD, does it exist?
If I have to explain what Electro-Static-Discharge is, and its danger to ESD sensitive aircraft parts, then this is probably not a blog for you; I’m going to avoid a long droning theoretical explanation of the phenomenon. Rather, I want to point out real world issues that hopefully heighten your awareness of the menace for your employees, and aid you in your training of the topic.
It is estimated that in today’s electronics environment, up to 60% of device failures are ESD caused1. This statistic is not for aviation alone, but for all electronics market segments. So, does it apply to aviation? I am not aware of any studies or statistics that could authoritatively address the question. Forensics to determine whether failures of aviation electronics are ESD-caused do exist, so why don’t we have a better handle on this peril? The fact is we can’t afford it. We want the failed part fixed and back in service as quickly as possible and at the lowest price. Otherwise, every Avionics Repair Station would have to be equipped with scanning electron microscopes and the specialized equipment to disassemble integrated circuits at the microscopic level in order to scan it for ESD damage…quite unlikely. To be clear, it is not being suggested that this level of forensics be applied to every failure in order to quantify the issue. What should be emphatic is that the degree of ESD caused failures is not routinely or authoritatively quantified, so the 60% figure may be applicable at best, or understated at worst. If so, how observant are your employees regarding ESD protective processes and procedures?

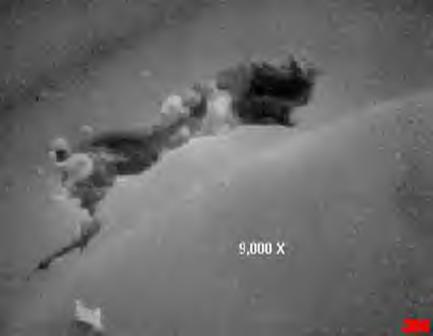
ESD sensitive parts that have been damaged will manifest such damage in one of several ways upon being installed on
the aircraft:
a) Immediate failure of the part when the component/system is tested.
b) The part fails much sooner than its designed Mean Time Between Failure (MTBF) figure.
c) The part exhibits intermittent or random failures.
For those you who are or have been avionics technicians, you absolutely abhor intermittent failures; the rule is it never fails when you’re working it, right?
Just as significant is the potential for ESD caused failures to contribute to a part becoming a rogue or chronic part due to its many as-yet uncorrected failures. This is tied to the part’s intermittent or random failures. There is another blog devoted exclusively to Chronic and Rogue parts; check it out at this link:
http://www.aviationsuppliers.org/index.asp?bid=222&BlogEntryID=19&FormID=300
A major factor contributing to ESD damage is lack of heightened awareness regarding the ease in which damage occurs. For example, the average person can feel a discharge on a doorknob if it is greater than 3500 volts; hear the discharge if it is greater than 5000 volts, and see it if it is greater than 8000 volts. By comparison, damage to integrated circuits occurs at fractions of those voltages. This means that the person imparting the damage will not have felt, seen or heard the discharge; nobody knows it occurred, and there will be no forensic investigation of the fact.
How about parts just removed from the aircraft? Do your Technicians immediately put on the ESD caps, or does the unit get shipped all the way to the repair shop sans caps? If so, they may have just raised your repair costs by causing additional damage not related to the removal reason. Ask your repair shops how often this occurs, it may surprise you.
Finally, I’ve got to say it, I have noticed that at Airlines, Repair Stations, and Distributors, there seems to be a lack of familiarization among internal quality auditors with their own published ESD procedures. If so, this too contributes to our lack of being able to quantify non-compliance and therefor its likely effect on product reliability and cost, and as we all know, we can’t fix what we can’t quantify, or can we?
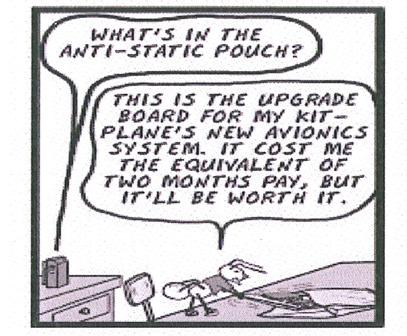
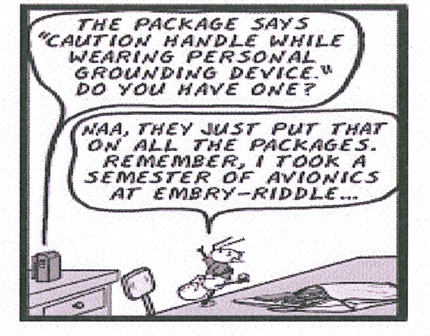
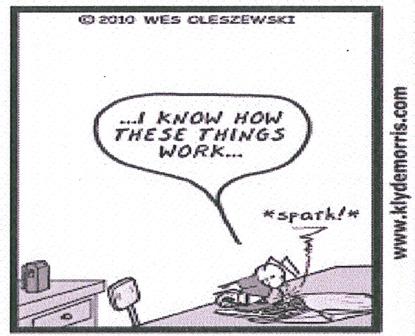
For the Distributor/Stockist community, I’m pleased to report the ASA is working on a Best Practice for ESD protection in the workplace; it will be available later this year. Of course there are many ESD Standards, but this no attempt to be a standard; rather a simple Best Practice document available exclusively for Distributor/Stockist operations.
For the novice, all this should be shocking; I’ll not remain static on the subject, I must discharge my duties.
Your comments left here are most welcome.
1ESD Control Handbook, Static Control Measures; 3M Corporation.
Roy RESTO
Fully Profiled on Linked-In
www.linkedin.com/in/royresto