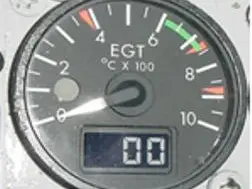
If you’re like me, you likely read the title as “Automatic” rather than “Autonomic”. On closer examination of the term, I had flashbacks to my youthful days in Biology class. For those physiology aficionados among us, the term “Autonomic Nervous System” will be familiar. The organs of our body, such as the heart, stomach and intestines, are regulated by a part of the nervous system called the autonomic nervous system (ANS). The ANS is part of the peripheral nervous system and it controls many organs and muscles within the body. In most situations, we are unaware of the workings of the ANS because it functions in an involuntary, subconscious reflexive manner. For example, we do not notice when blood vessels change size or when our heart beats faster. In other words, the ANS works behind the scenes of our conscious to keep things regulated largely without our manual intervention. And so it is with Autonomic Logistics.
I’m writing this blog because the F-35 Joint Strike Fighter is being fielded with what is being heralded as an advanced Autonomic Logistics Information System (ALIS). If so, the model will be a harbinger of logistics systems that will cascade into civilian uses. The fundamental elements of Autonomic Logistics are not new. ALIS has built upon those fundamental elements significantly, which is the basis for its attention – getting innovations, but I have gotten ahead of the story. An essential cornerstone element of the system is a concept known as Predictive Maintenance, PM (PM is called different names by different sources but for ease of reference we’ll just use PM). What follows is a historical perspective and introduction to PM.
HISTORICAL AND INTRODUCTORY OVERVIEW OF PM:
Simply put, PM systems should be able to predict the failure of an aircraft part before it happens, and will be tied to a specific part on a specific tail number. Cool, huh?
In fact, the concept is not new. Past concepts in PM were pioneered by the airlines and engine manufacturers. A typical scenario follows.
Most turbine engine designs include provisions for monitoring an engine’s EGT, or Exhaust Gas temperature; a critical measure of the performance of the engine, among others. The information is presented to the flight crew for monitoring. Of course there are lower and upper limits for EGT for a given engine operating profile. This data is tapped, digitized, and then transmitted during flight by a system called ACARS (Arinc/Aircraft Communication And Reporting System). ACARS transmitted information is then received on the ground and sent to the airline’s Maintenance Operations Control center for analysis. A graph for that engine may reveal that the EGT during the last week is starting to creep toward the upper limit; an indication of a deteriorating condition, that if left un-addressed could cause an interruption in that aircraft’s schedule, or worse, an unexpected engine change, diversion, or cancellation. At this time, the airline would dispatch mechanics to the aircraft at an overnight maintenance station to perform a borescope inspection, and to take the appropriate action ahead of the failure, an infinitely more manageable situation than an unexpected failure. The concept started to be applied to other systems besides engine installations, by Boeing and Airbus among others.
The question is, what data is available on board the aircraft for transmission to the ground for PM analysis? An early consideration was the data already being collected by the Flight Data Recorders (FDR’s). Although some of it may be of the type usable for PM programs, it was not designed specifically for that purpose. Aircraft systems are currently being designed to output information that are suitable for PM programs. Early examples of these systems included Boeing’s Aircraft Health Monitoring System (AHM), Airbus’s Aircraft Condition Monitoring System (ACMS/AIRMAN), and HUMS, Health and Usage Monitoring Systems used and developed by various firms for Helicopters.
Airplane Health Monitoring (AHM): Boeing
AHM offers “anticipation” of maintenance needs in real time and noticeably improves dispatch reliability. During flight, aircraft problems are detected and relayed in real time to the ground where they are analyzed for severity, parts availability, and scheduling.
American, Air France, and Japan Airlines helped develop the beta test software. AHM is expected to provide a 15% reduction in schedule interruptions and a 10% or greater lowering of NFF (No Fault Found) actions on average.
Tools of the Future. Air Transport World, February 2005, p. 57 |
AIRcraft Maintenance ANalysis: Airbus
Typically uses Fault Monitoring and Diagnostics undertaken by the Built In Test Equipment (BITE) of each system. The data is downloaded in real time via data link to the airline ground stations where it is analyzed for severity, parts availability, and scheduling.
The AIRMAN system has been estimated to provide a cost reduction of $4 USD per flight hour, and a decrease of 10 minutes in maintenance actions.
Tools of the Future. Air Transport World, February 2005, p. 57 |
Notice that both manufacturers are attempting to quantify the estimated savings of the systems, this because currently these systems would require an investment by the airline to make it work. If you do the math, for a large airline the savings could indeed be significant.
PM: What’s needed?
- Aircraft systems designed to output information on its internal condition
- Aircraft to satellite, to ground station transmission of the data
- Software systems designed to process the data
Airline Maintenance Engineering operations have departments to monitor “Reliability” trends. For example, if component removals from aircraft for a certain ATA chapter start to trend negatively, flags are raised to attract attention to the causes. This is a classic statistical monitoring system. Reliability programs can predict that during a given period of flight hours you’re going to have given amounts of removals, but it cannot tell you when, or to what components it will happen. Enter PM programs as described.
To summarize, PM programs can provide:
- On a micro scale, early warnings of deteriorating equipment tied to tail numbers or engine serial numbers
- On a macro scale, the resultant data can more accurately predict future maintenance requirements
- On both scales, PM allows maintenance planners to more proactively and accurately plan and position spare parts
- Allocate required maintenance technicians more efficiently
- Allocate tools and test equipment more efficiently
And that’s the historical as well as introductory overview of PM. Whatever you call it, the OEM’s have continuously built upon PM concepts and integrated it into management, engineering, operations, and logistics processes. Such is the case with the F-35 Autonomic Logistics Information System, which seems to have taken these concepts to its current, advanced concept.
According to Lockheed Martin,
"ALIS integrates a broad range of capabilities including operations, maintenance, prognostics, supply chain, customer support services, training and technical data. A single, secure information environment provides users with up-to-date information on any of these areas using web-enabled applications on a distributed network.
ALIS will serve as the information infrastructure for the F-35, transmitting aircraft health and maintenance action information to the appropriate users on a globally-distributed network to technicians worldwide.
ALIS receives Health Reporting Codes while the F-35 is still in flight via an RF downlink. The system enables the pre-positioning of parts and qualified maintainers on the ground, so that, when the aircraft lands, downtime is minimized and efficiency is increased.
ALIS allows the F-35 systems to deliver operational and training execution with innovative technologies that meet the demands of everyday use."
- Single, Secure Information Environment
- Distributed Network Based on Web Technologies
- Capabilities Integrate Broad Range of Domains
- Operations
- Maintenance
- Supply Chain
- Customer Support Services
- Training
- Tech Data
- External Interfaces
- Integrated COTS/developed solutions utilizing best in class applications
- Support is in place today to support the development and test of the first production aircraft.
- Service oriented architecture allows for reach back to legacy systems and future IT initiatives
- Key enabler supporting Performance Based Logistics (PBL) for the F-35”1
But what about the “Autonomic” in ALIS?
ALIS reduces logistic delay times by automatically generating appropriate actions with notice to system managers, just as the human nervous system operates the body with unconscious control by the brain.
"Each F-35 will constantly monitor its own systems and automatically relay information to ALIS. In turn, ALIS will provide an information infrastructure that captures, analyzes, identifies and communicates F-35 characteristics and data, providing information and decision support for every Lightning II user worldwide, on land or at sea," said Kimberly Gavaletz, Lockheed Martin vice president for F-35 Autonomic Logistics and Global Sustainment.
In the commercial world, integrating PM with Logistics is gradually gaining acceptance whether the aircraft you fly are Boeing, Airbus, Business or Helicopters. The programs being offered for such management programs remain largely an option for the operator, and in fact have only been applied by most operators to a given, relatively small fleet. ALIS on the other hand, will not be optional; it will be integrated with the product aircraft, and the most interesting and challenging aspect is that there are expected to be as many as 4,500 aircraft, a huge fleet compared to commercial operators. Companies involved in any aspect of the ALIS logistics chain, whether manufacturing, distribution, or MRO can expect unprecedented access to information regarding the ‘big picture’; information that is real-time, predictive, and empowering.
In summary, the primary reasons to monitor the implementation of ALIS are its autonomic features, that it is not optional, and that it will apply to an entire fleet, as many as 4,500 aircraft; it encompasses advanced features on a huge scale. As far as the historical chronology of the development of Predictive Maintenance-Logistics systems goes, ALIS will no doubt be looked upon as a major contributor.
1 http://www.lockheedmartin.com/us/products/ALIS.html